HEAVY MEDIA DRUM
The Heavy Media Drum (HMD) consisting of a cylindrical drum with conical sections on each end, feed chute, sinks launder and perforated lifters is used for heavy media separation of feed materials within a size range of 10 – 300mm.
Product
Description
The Heavy Media Drum (HMD) consisting of a cylindrical drum with conical sections on each end, feed chute, sinks launder and perforated lifters is used for heavy media separation of feed materials within a size range of 10 – 300mm. The drum rotates on two forged steel tyres located on the outer circumference of the drum. The drum is supposed on four steel roller assemblies. Lateral movement of the drum is controlled via thrust rollers positioned on each side of one of the steel tyres.
The drum is driven by a gearbox coupled to an electric motor vis V-belts mounted on a removable drum base. Other drive components include drive, driven sprockets segments mounted on the outer circumferences of the drum shell to provide a positive drive to rotate the drum at a predetermined speed to suit the specific application.
All internal components, namely feed chute, sinks launder, rigid and flexible skirts and medium pipework are mounted independently of the drum by two horizontal support beams which are connected on each end by upright supports.
HEAVY MEDIA DRUM
The Heavy Media Drum (HMD) consisting of a cylindrical drum with conical sections on each end, feed chute, sinks launder and perforated lifters is used for heavy media separation of feed materials within a size range of 10 – 300mm.
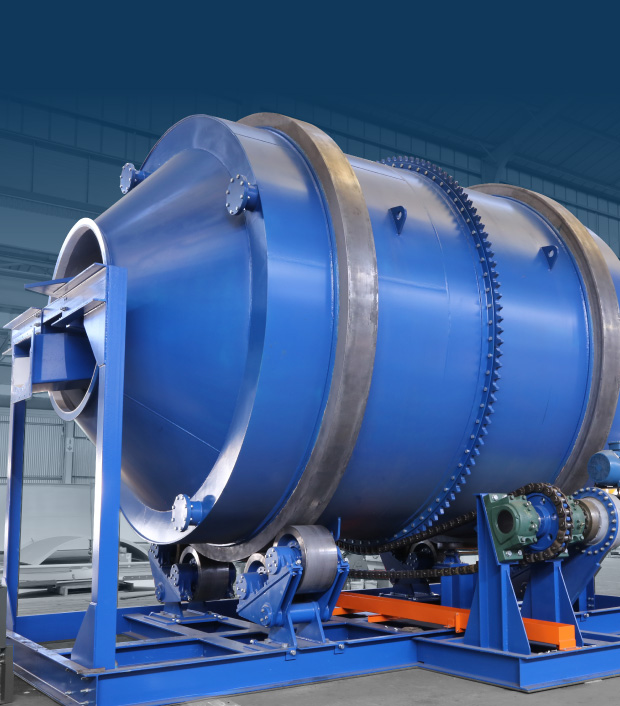
Product
Description
The Heavy Media Drum (HMD) consisting of a cylindrical drum with conical sections on each end, feed chute, sinks launder and perforated lifters is used for heavy media separation of feed materials within a size range of 10 – 300mm. The drum rotates on two forged steel tyres located on the outer circumference of the drum. The drum is supposed on four steel roller assemblies. Lateral movement of the drum is controlled via thrust rollers positioned on each side of one of the steel tyres.
The drum is driven by a gearbox coupled to an electric motor vis V-belts mounted on a removable drum base. Other drive components include drive, driven sprockets segments mounted on the outer circumferences of the drum shell to provide a positive drive to rotate the drum at a predetermined speed to suit the specific application.
All internal components, namely feed chute, sinks launder, rigid and flexible skirts and medium pipework are mounted independently of the drum by two horizontal support beams which are connected on each end by upright supports.
OPERATIONAL THEORY
Media of the appropriate density is fed into the pool area of the Heavy media Drum via the feed chute, the curtain medium inlet which reports behind the “ downside” flexible rubber skirt and the push medium inlet which assists the sinks material from the exiting the drum.
As a result of the differing densities of the feed, separation occurs in the pool area of the drum. The less dense particles will float and exit via the overflow weir were they report to a drain and rinse screen to recover the drum medium, whilst the denser particles sink to the bottom of the drum and are transported by perforated lifters fixed to the inside of the drum and are discharged into the sinks launder.
The sinks material exits the drum via the sinks launder inlet. This material will report to a screen for draining and rinsing to recover the drum media. All media recovered from the drain and rinse screens is re-introduced back into the HMB on a continuous basis once the medium’s density has been corrected.
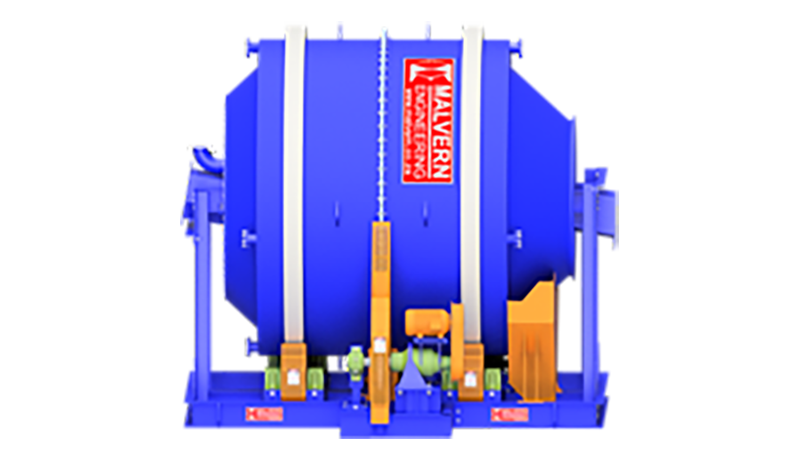
PROCESS CONSIDERATIONS
The following points should be borne in mind
when considering a Heavy Medium Drum:
- The effectiveness of the separation is dependent upon the difference in the specific gravity of the materials which are to be separated (sinks and floats).
- The particle sizes to be separated. Smaller particles require a longer period of time in the drum to achieve the required separation, than larger particles. The greater the percentage of fine material in the feed, the more difficult it will be to achieve the desired separation.
- The rates at which particles float or sink
- The amount of near gravity material ( material whose density is close to that of the separating density) in the feed. The greater the percentage of near gravity material in the feed, the more difficult it will be to achieve the desired separation.
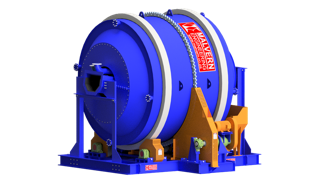
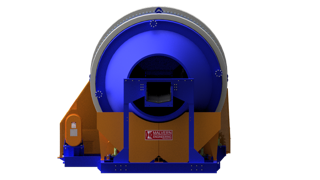
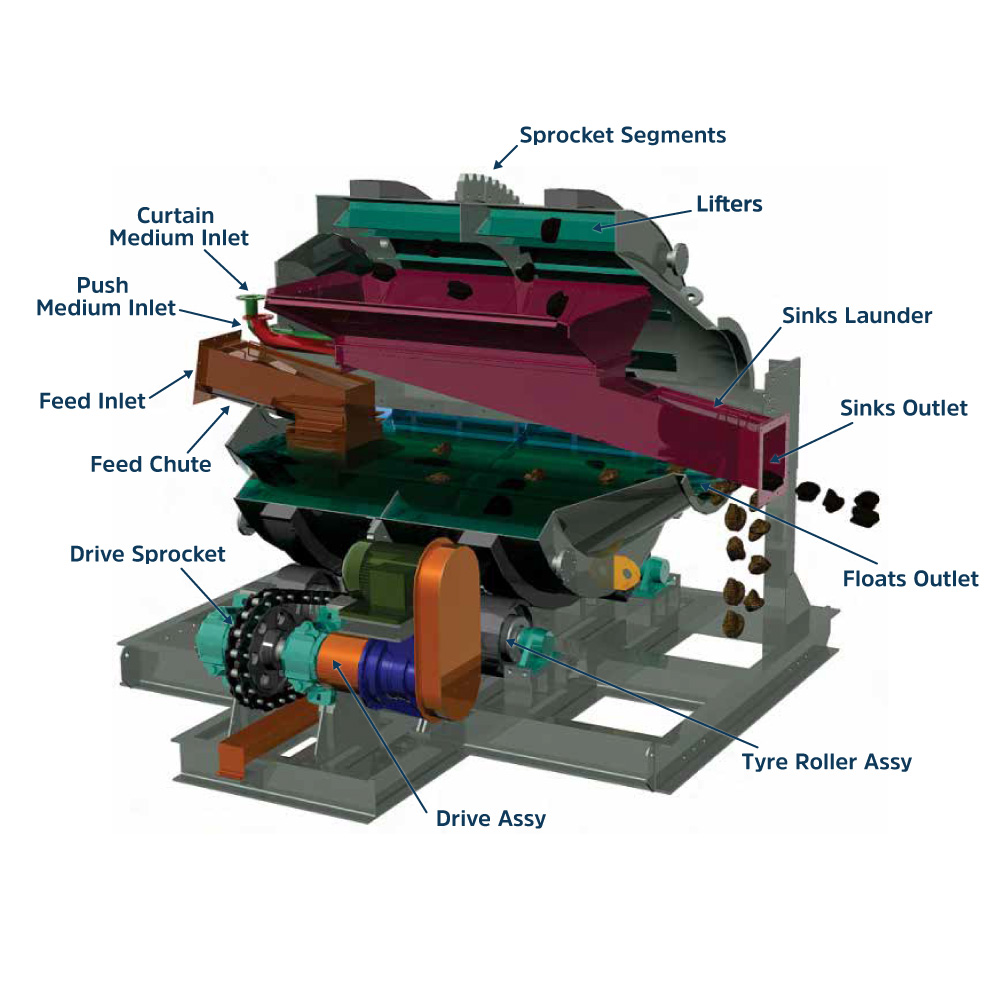
Design
Features
- Easily Accessible Drive System
- Superior Wear Materials
- High Capacity
- High Efficiency
- Designed with Safety in mind
Design
Features
- Easily Accessible Drive System
- Superior Wear Materials
- High Capacity
- High Efficiency
- Designed with Safety in mind
Benefits
- Variation of Feed Quality
- High Availability
- Simple Rugged Design
- Sharp Separation
- Minimal Maintenance Cost
- Site Service Support
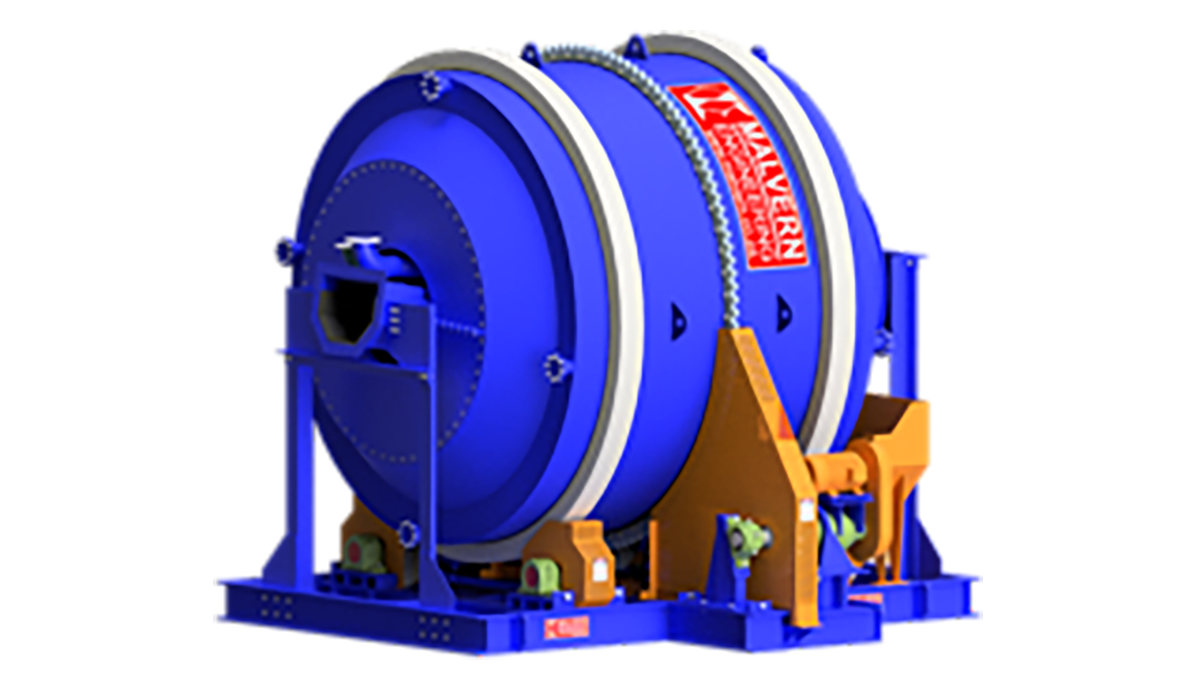
Design Criteria
- Feed rate (tph)
- Feed Particle Density (t/m3)
- Top Size of Material (mm)
- Yield to Sinks (% on mass basis)
- Sinks Particle Density (t/m3)
- Sink Bulk Density (t/m3)
- Floats Density (t/m3)
Benefits
- Feed rate (tph)
- Feed Particle Density (t/m3)
- Top Size of Material (mm)
- Yield to Sinks (% on mass basis)
- Sinks Particle Density (t/m3)
- Sink Bulk Density (t/m3)
- Floats Density (t/m3)
HEAVY MEDIA DRUM SPECIFICATIONS FOR COAL
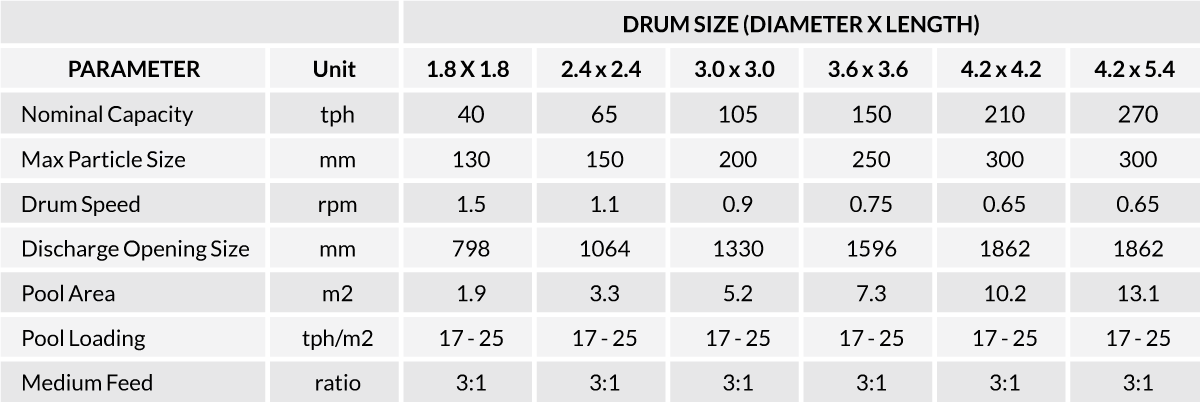